What are Geiss Vacuum Forming Machines
Geiss AG offer two types of bespoke Vacuum Forming Machines, either the T11 or the Ts1 and both can be individually equipped to suit your production requirements.
The basic machine consists of a rigid frame construction with a closed machine chamber, equipped with servo motor drives, adjustable clamp frame, automatic sheet sag control, individually controllable top and bottom heaters, swivel PC control panel, plug assist and cooling fans with water spray mist.
In comparison to the conventional, pneumatically operated systems, Geiss machines have the advantage of their newly designed ‘Drive Technology’ with a highly dynamic design, which will reduce machine cycle times by approximately 60%, leading to a 50% reduction of energy consumption.
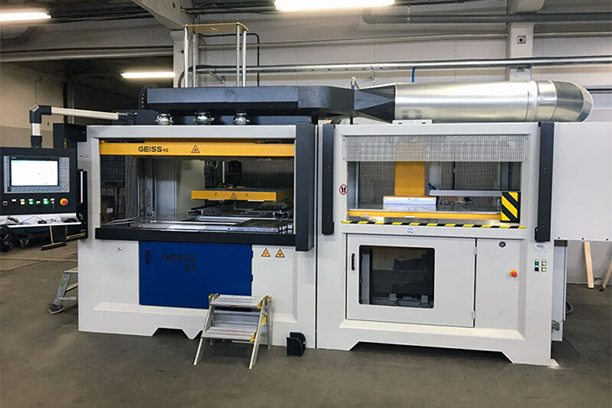
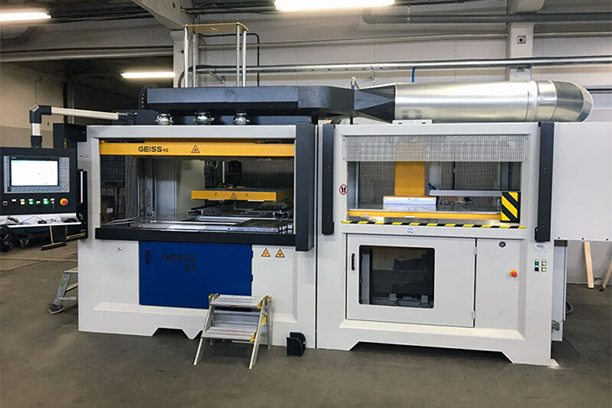
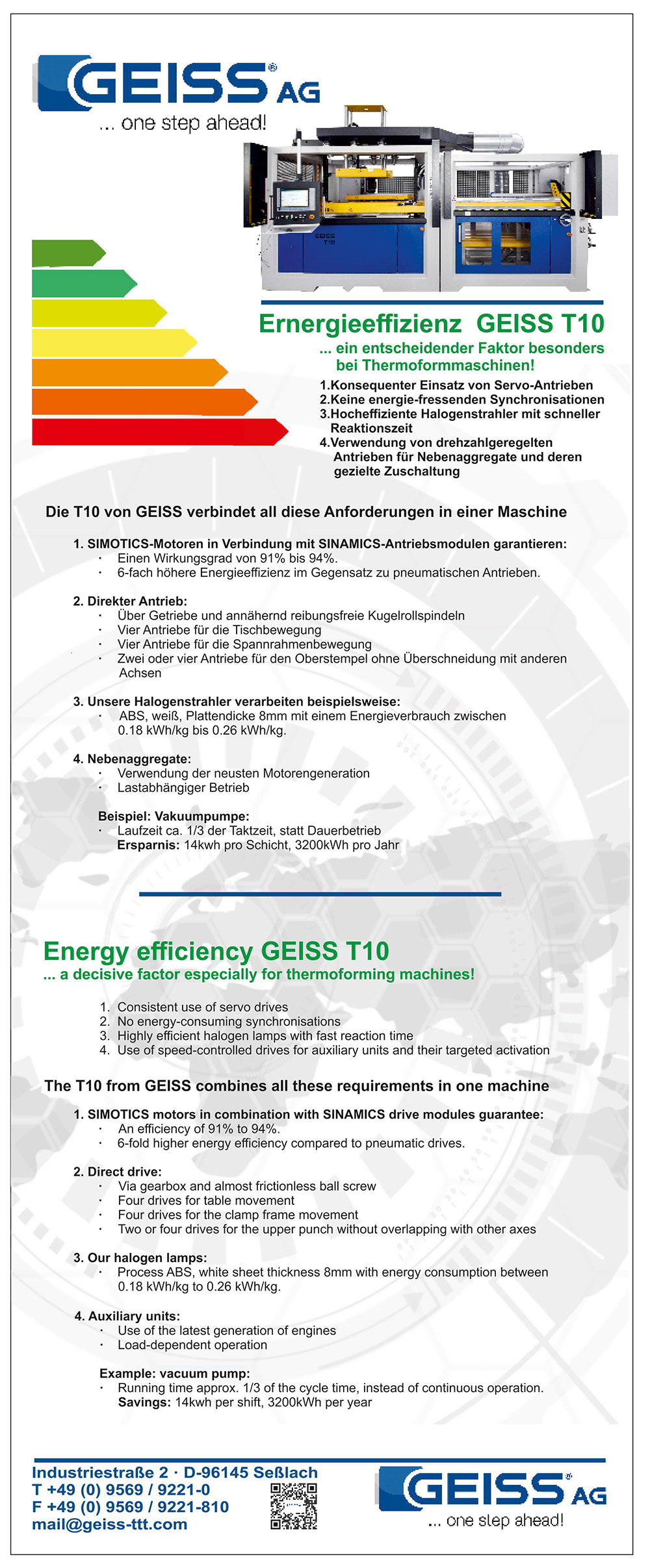
Geiss T11 Thermoforming Machine
Up to 50% Productivity Increase in Thermoforming
The close cooperation between Siemens and Geiss AG saw the development of the new T11 vacuum forming machine. The basis of this series is built on the foundations of innovative automation and drive solutions as well as the Siemens TIA Portal. The new machine concept now takes less time to install and commission, boasts high precision and production quality, advanced process reliability and a staggering productivity increase of up to 50%. See for yourself!
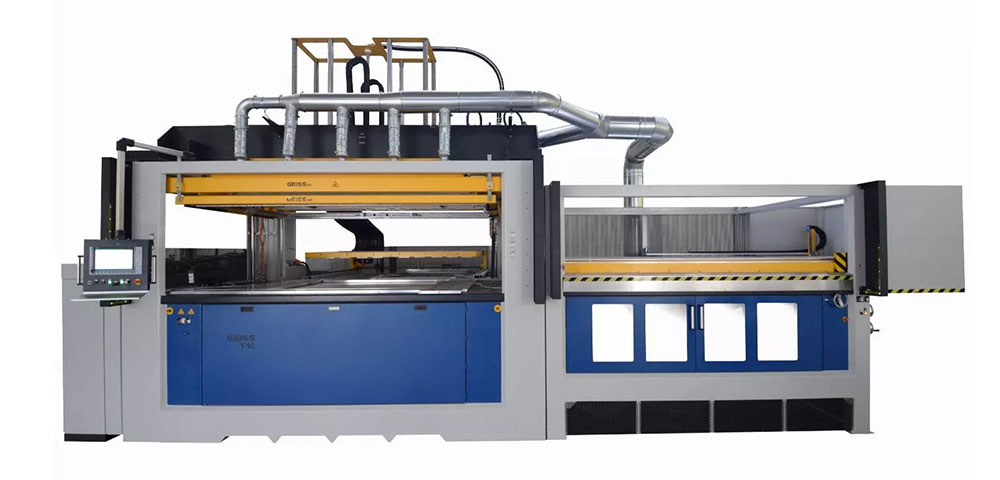
The basic T11 machine is equipped with the following items as standard, compared to previous T9 Machines:
Machine Characteristics of this vacuum forming machine:
- Servo Motor Driven Table, Plug Assist, Clamp Frame and Top & Bottom Heater
- Table Middle Position
- Clamp Frame Closing Delay (for the processing of acrylic materials)
- All Servo Valves for the main Axes
- All Programmable Positions for Main Axes
Improved Benefits such as:
- 60% faster Machine Cycle
- 30% faster Cooling Times
- High Repeat Accuracy, resulting in less Scrap Waste
- Lower Power Consumption
- Lower Compressed Air Consumption
- Increased Overall Performance
- Smaller Footprint
Bespoke Built Vacuum Forming Machines
Most Geiss Machines are of a bespoke design to meet the customer requirement. Occasionally, we have standard sized machines in stock. Please contact the office for more information
Contact Us
Geiss Ts1 Thermoforming Machine
Geiss offer thermoforming machines in the ‘Ts Series’, which have a shallow draw depth range (previously known as the U machine) and the ‘T Series’ which offer a deeper draw type machine.
The machines essentially consist of a closed machine chamber, equipped with adjustable clamping frames, individually controlled heating elements for top and bottom heater, PC control panel, plug assist and cooling fans with water spray cooling.
Common features of the series Ts1 and T:
- All machines are certified to CE Standard.
- No Platform required due to the ideal working height.
- Geiss guarantee the processing of any thermoplastic materials in any thickness, independent of optional equipment on the machine.
- The extensive list of additional options for both series allows for preferred customisation and automation. Any adjustment is possible, be it to increase the degree of automation or flexibility, or the reduction of tool change over times.
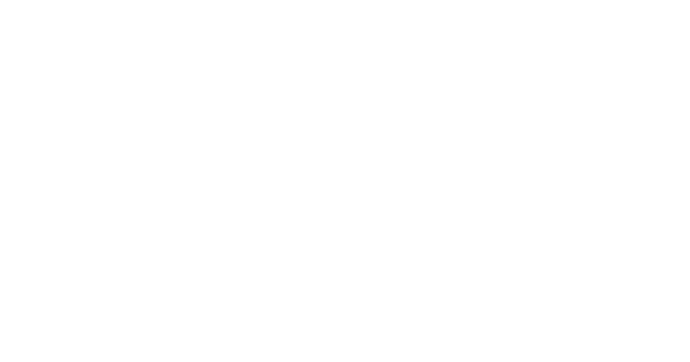
Siemens Control Systems & Standard Specifications
T Range – Deep Draw
Worldwide, the T series – developed in-house at Geiss – is now regarded as the standard for deep draw depths (the “T” stands for deep, which comes from the German word “tief”).
The T type machine is also the basis for Pressure & Twinsheet Forming Equipment to which the necessary options would be added to transform it into the Machine type you require!
The construction design as well as the large inner area of these heavy-duty universal forming machines allows customising with any of the additional GEISS options.
This makes the T series one of the most advanced high-tech solutions in the thermoforming sector.
Geiss Custom Machines
Contact Us
Address:
Unit 16, Cedar Court
Halesfield 17, Telford
Shropshire
TF7 4PF
Telephone:
Opening Times:
Monday – Thursday: 8:30 – 16:30 pm
Friday: 8:30 – 15:30 pm
Contact Us
Address:
Unit 16, Cedar Court
Halesfield 17, Telford
Shropshire
TF7 4PF
Telephone:
Opening Times:
Monday – Thursday: 8:30 – 16:30 pm
Friday: 8:30 – 15:30 pm